Steps to Develop a Quality Management System for ISO Certification
- isocertificationin51
- Jan 10, 2024
- 2 min read
Steps to Develop a Quality Management System for ISO Certification ISO certification is a prestigious recognition that demonstrates an organization's commitment to quality management systems. Developing a quality management system that meets ISO standards requires careful planning and implementation. Here are the steps to guide you through the process: 1. Understand ISO Standards: Familiarize yourself with the ISO standards relevant to your industry. For example, ISO 9001 is the standard for quality management systems. Understand the requirements and how they apply to your organization. 2. Conduct a Gap Analysis: Assess your current processes and identify areas that need improvement to meet ISO standards. This analysis will help you understand the gaps between your existing system and the requirements. It will serve as a roadmap for developing your quality management system. 3. Establish Objectives and Policies: Define your organization's quality objectives and develop policies that align with ISO standards. These objectives should be measurable, achievable, and aligned with your business goals. Clearly communicate these objectives and policies to all employees. 4. Document Procedures: Document all the processes and procedures within your organization that are relevant to quality management. This includes processes for product/service development, purchasing, production, and customer service. Ensure that these documents are easily accessible to all employees. 5. Implement Controls: Put in place controls to ensure that your processes are being followed consistently. This may include training employees on the procedures, implementing quality checks at various stages, and establishing corrective action procedures. Regularly review and update these controls as needed. 6. Monitor and Measure: Regularly monitor and measure your processes to ensure they are meeting the desired outcomes. This can be done through internal audits, customer feedback, and performance indicators. Use this data to identify areas for improvement and take corrective actions when necessary. 7. Continual Improvement: Continuously seek opportunities for improvement within your quality management system. This can be achieved through analyzing data, conducting management reviews, and implementing corrective actions. Encourage employee involvement and feedback to drive innovation and improvement. 8. Prepare for Certification: Once your quality management system is fully implemented and functioning effectively, you can engage a certification body to conduct an audit and assess your compliance with ISO standards. Prepare all the necessary documentation and evidence to demonstrate your adherence to the standards. By following these steps, you can develop a robust quality management system that meets ISO standards and positions your organization for ISO certification. Remember that ISO certification is not a one-time achievement but an ongoing commitment to quality and continuous improvement.
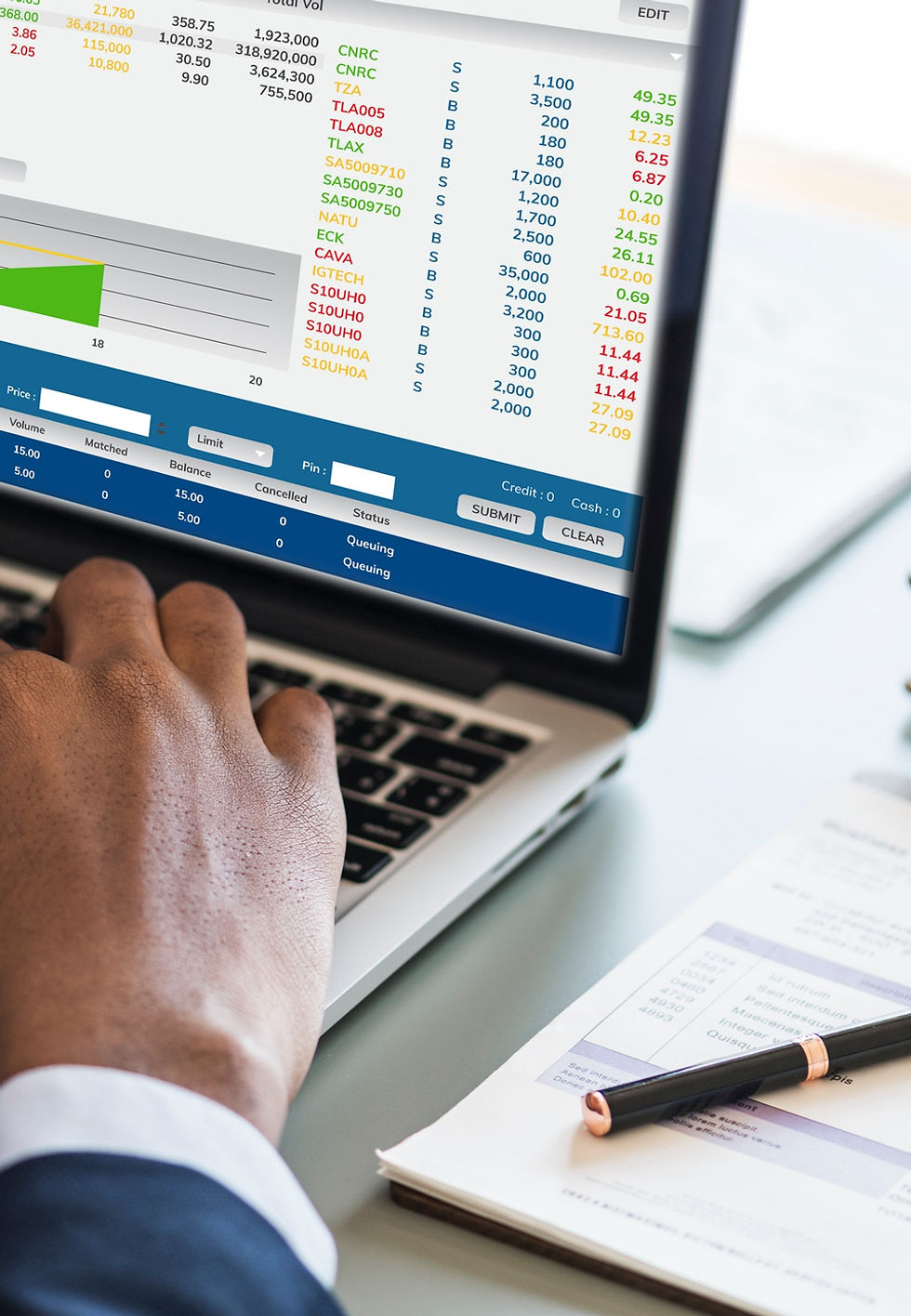
Comments